Poultry Care
Cannon Republic provides beneficial biology that plays a crucial role in the production of poultry by helping maintain the health and well-being of the birds, improving growth rates, and reducing the risk of disease outbreaks. Here are some of the ways beneficial biology can impact poultry production:
Digestive Health
Poultry require a nutritious balanced diet to thrive, and beneficial microbes play a key role in supporting digestive health. Beneficial microbes help break down food, improve nutrient absorption, and reduce the risk of digestive problems like diarrhea.
Immune System Function
Poultry are susceptible to a wide range of diseases, and a healthy immune system is crucial for preventing and fighting off infections. Beneficial microbes help to support the immune system by stimulating the production of antibodies and other immune cells.
Growth Promotion
Beneficial microbiology helps break down feed more efficiently, makes nutrients more available, improves growth rates, and leads to larger more robust birds.
Disease Prevention
Beneficial microbiology helps prevent the growth of harmful bacteria in the poultry’s gut, reduces the risk of disease outbreaks, lowers mortality rates, and improves overall health of birds.
Odor Control and Solids Reduction – Chicken Processing Plant
The Problem
A chicken processing plant in Southeastern US has a 1.2 million gallon per day wastewater stream. The wastewater treatment system consists of a series of 4 ponds, all of which are anaerobic. The wastewater travels from the first pond to the second through a gravity feed system. From the second pond the water is pumped to ponds three and four. The plant has a wastewater land application permit and the water from ponds three and four is pump to irrigation guns which spray the wastewater onto hay fields. Two major problems existed. The solids (mostly grease, fats, and feathers) cap built up on the first pond had reached levels of 24” to a maximum of 42” and the retention capacity of the pond was greatly diminished. The plant was also experiencing major odor problems being generated at the irrigation guns during the land application. The odors were hydrogen sulfide as well as ammonia in origin.
The Solution
Ponds two, three, and four were shocked with a total of 500 gallons of Humate BR-10. The CR Foundation BR-10 was applied with the use of a high-pressure pump and fire hose to each pond. CR Foundation BR-10 was metered into the system with a continuous feed pump just as the wastewater leaves the plant and before the water discharged into pond one at a rate of 37 PPM of the daily flow of 1.2 million gallons. (Approximately 45 gallons per day.)
Conclusion
Within 72 hours after treatment started the H2S and ammonia odors at the irrigation guns were eliminated. At the end of 30 days the grease and fat cap on pond one was reduced by an average of 47%.
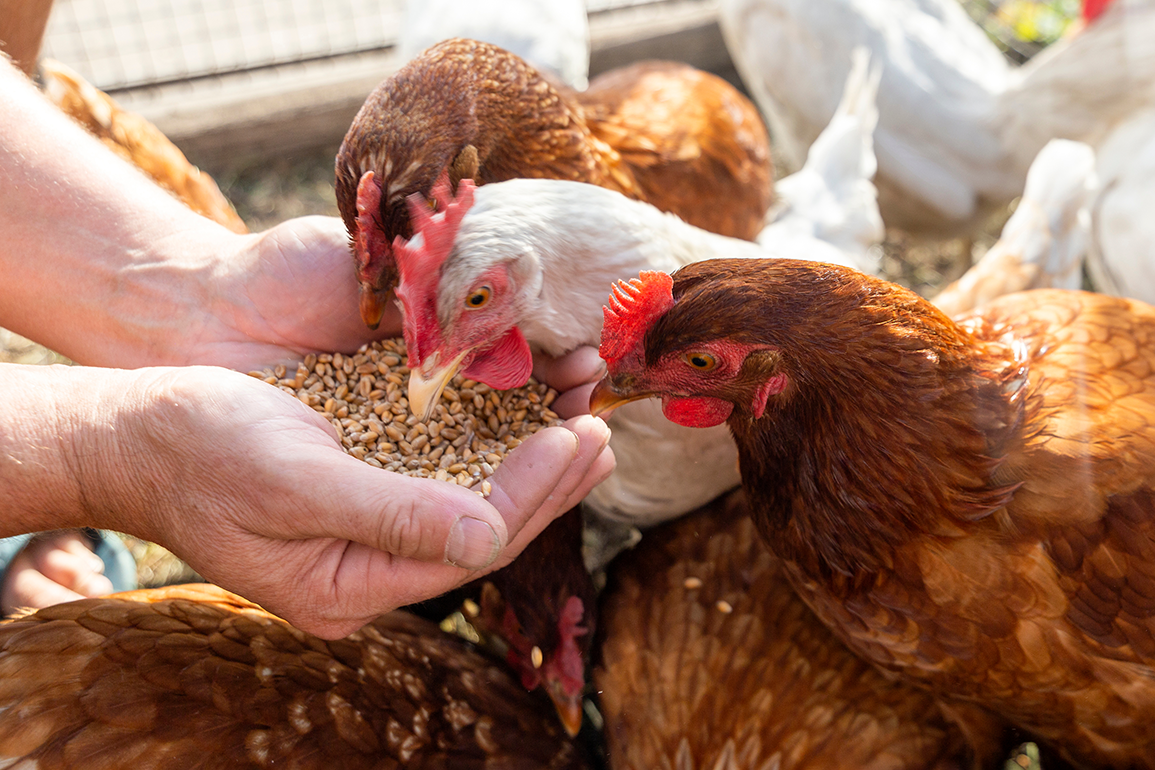
TSS, BOD, Ammonia, Hydrogen Sulfide, and Sludge Reduction – Chicken Processing Plant
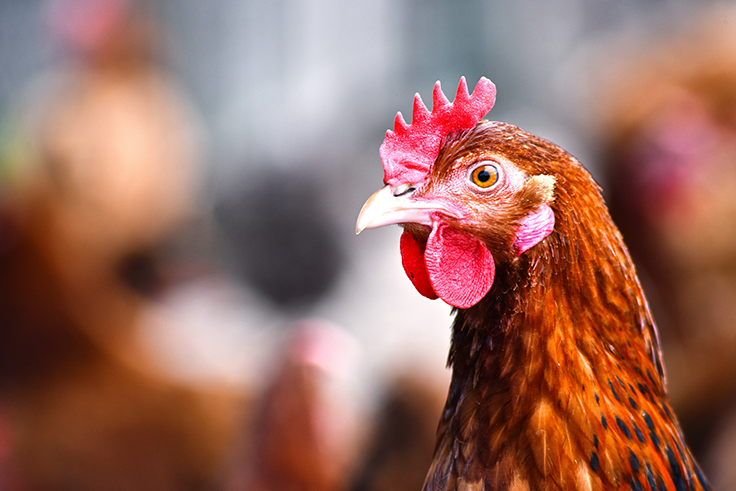
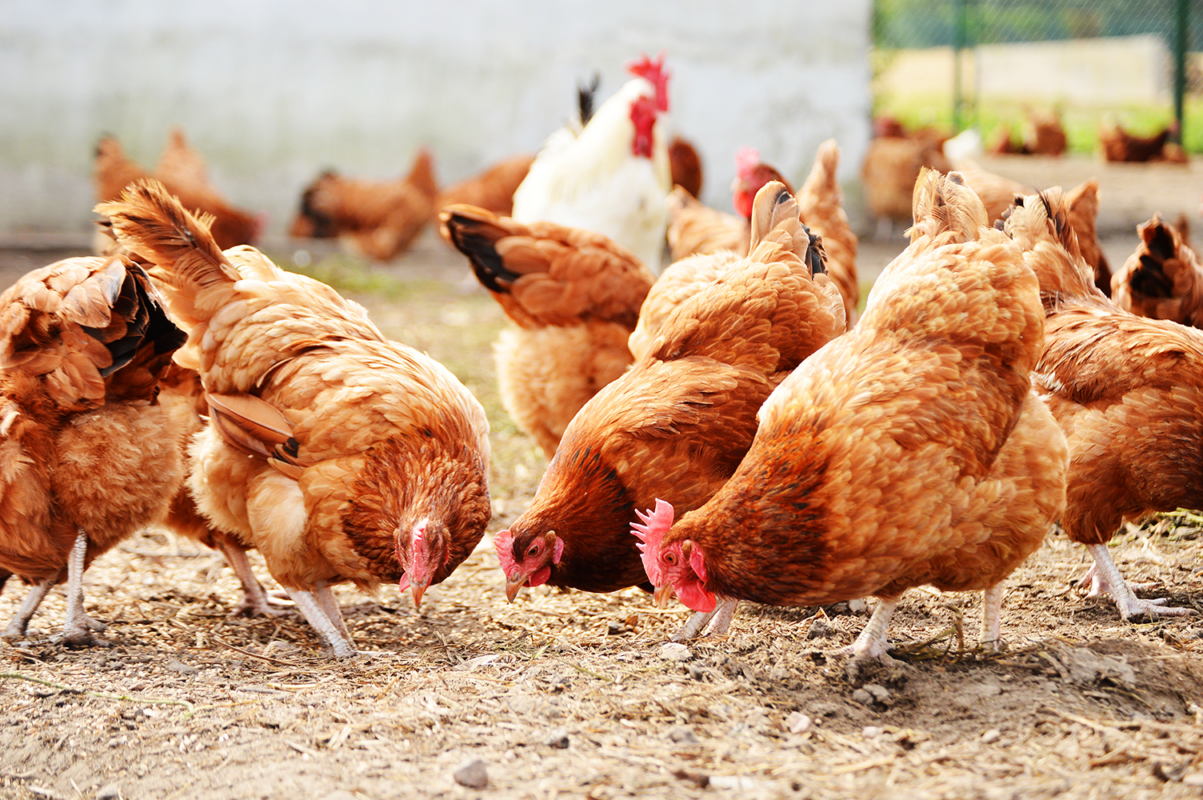
The Problem
A large chicken processing and rendering plant in Southeast US was faced with numerous problems associated with the treatment of wastewater at the plant. The plant has a daily flow of 1.8 million gallons of water. The primary issue was the build-up of a layer of heavy fats, grease and oil on the surface of a 10,000-gallon grease trap located down-line from the rendering building. The solids build up on the surface of this grease pit would exceed 2.5 feet and forced the plant operators to physically remove the cap with a backhoe once the thickness of cap began to reach the overflow level of the pit. The second issue was high TSS (750-1100 ppm), COD/BOD (1400-1800 ppm), and ammonia nitrogen (50-70 ppm) levels in the plants two aeration ponds. These ponds are in sequence with the first pond having a capacity of 4.5 million gallons and the second having a capacity of 14 million gallons. The plant has a land application permits which allows for irrigation of hay fields with the treated wastewater. The third problem resulted with high H2S levels being generated by the aeration ponds.
The Solution
To address the sludge cap problem on the grease pit CR Foundation BR-10 was applied through a pressure sprayer at a rate of 8-ounces per gallon directly onto the surface of the cap. One quart of concentrated product was applied per treatment. The cap was treated twice each day. Within 7 days the cap was reduced to approximately 5 inches of tan foam. Treatment continues at the same rate twice daily. To address the TSS, COD/BOD, ammonia nitrogen, and hydrogen sulfide problems in the aerated ponds CR Foundation BR-10 was the recommended product. Pond #1 (4.5-million-gallon capacity) was shocked with 75 gallons (17 ppm) and Pond #2 (14-million-gallon capacity) was shocked with 175 gallons (12 ppm). The shock treatment was applied with a high-pressure hose to provide a more uniform coverage of the pond surface area and allow for better blending of the product into the wastewater. A daily maintenance program was implemented where 5-gallons (2.8 ppm of the daily flow rate) of CR Foundation BR-10 would be metered into pond #1 at the influent point. There was a significant reduction in hydrogen sulfide odors with 48 hours of treatment. After 30 days of treatment the TSS and COD/BOD levels on average were reduced by 60-65%. The ammonia nitrogen levels were reduced by approximately 85%. (See charts on following pages). The maintenance application rate of 5 gallons per day continues.
Conclusion
The CR Foundation BR-10 used in this application far exceeded original expectations.
Poultry Operations
Microbiology can play several beneficial roles in reducing the amount of ammonia produced in poultry operations. Ammonia is a common byproduct of poultry waste and can be harmful to the birds’ respiratory health, as well as to the environment. Here are some of the ways that microbiology can help to reduce ammonia production:
Microbial Inoculants
Microbial inoculants, such as bacteria or fungi, can be added to the litter in poultry houses. These microorganisms can help to break down the organic matter in the litter more efficiently, reducing the amount of ammonia produced.
Probiotics
Probiotics can be added to poultry feed to promote gut health and improve digestion. By improving the efficiency of feed conversion, probiotics can help to reduce the amount of waste produced and the amount of ammonia in the litter.
Nutrient Management
Microbiology can also play a role in managing nutrients in poultry litter. By optimizing the ratio of carbon to nitrogen in the litter, microbial activity can be enhanced, leading to more efficient breakdown of organic matter and less ammonia production.